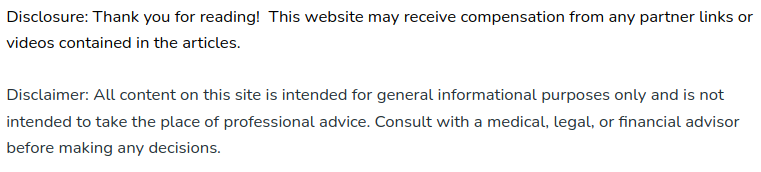
Tank cleaning is an essential maintenance task that ensures equipment longevity and operational safety. Regular cleaning prevents the accumulation of hazardous materials and maintains the efficiency of industrial operations. In Ohio, tank cleaning is crucial for abiding by safety regulations and ensuring environmental protection.
What is the Best Method for Tank Cleaning OH?
Overview of Different Tank Cleaning Methods
Tank cleaning methods can be classified into manual, automatic, and semi-automatic techniques. Manual cleaning is often labor-intensive but provides thorough cleaning results. Automatic systems, such as Clean-in-Place (CIP) systems, enhance efficiency by minimizing human intervention.
Semi-automatic cleaning methods offer a balance between manual labor and automation, making them ideal for medium-sized tanks. These methods often involve less downtime compared to manual cleaning and provide relatively thorough results. The choice of method varies significantly based on the industry and specific tank requirements.
In Ohio, industries are increasingly turning to automatic systems due to their ability to reduce labor costs and enhance cleaning efficiency. The availability of modern technology facilitates the implementation of these systems in various industrial sectors. However, the method chosen often depends on specific operational needs and the nature of the contaminants.
Factors to Consider When Choosing a Cleaning Method
Tank size is a crucial factor in determining the appropriate cleaning method as larger tanks often benefit from automated systems. The type of contaminants present also influences the choice, with corrosive materials requiring specialized cleaning solutions. Environmental considerations are equally important, with stricter regulations necessitating eco-friendly cleaning solutions.
In Ohio, industries must adhere to local environmental regulations when selecting cleaning methods. Balancing effectiveness, cost, and sustainability is key in making an informed decision. Regulatory compliance not only ensures safety but also minimizes the negative impact on the environment.
Businesses also need to consider the operational downtime associated with each cleaning method. Automated solutions often result in reduced downtime, thereby enhancing productivity. Overall, selecting the suitable method involves a careful assessment of these multiple factors.
Pros and Cons of Common Tank Cleaning Methods
Manual cleaning, while thorough, is often time-consuming and labor-intensive, making it less feasible for large-scale operations. Automated systems offer the advantage of speed and reduced manpower requirements but can be costly to install. Semi-automatic methods combine aspects of both, offering a balance between efficiency and cost.
The cost of implementing automated systems can initially be high, but their long-term benefits often outweigh these costs. They reduce human error and offer consistent cleaning performance, which is vital for high-demand industries. Manual methods, though cheaper, can sometimes lead to inconsistent results.
In Ohio, factors such as local labor costs and the prevalence of certain tank sizes influence the choice of cleaning methods. Automated methods are gaining popularity due to their efficiency and reliability, particularly in sectors like food processing and chemical manufacturing. However, small businesses may still prefer manual or semi-automatic methods due to budget constraints.
How Often Should Tanks Be Cleaned in Ohio?
Regulatory Guidelines and Industry Standards
Ohio’s tank cleaning guidelines emphasize periodic maintenance to ensure safety and compliance. Industry standards often dictate the frequency of cleaning based on the specific type of industry and the substances stored. Regular inspections are often mandated by state regulations to assess cleaning needs.
State guidelines aim to prevent contamination and maintain operational efficiency in industries reliant on storage tanks. By adhering to these guidelines, businesses can avoid potential fines and ensure their operations align with best practices. Regulatory compliance plays a crucial role in maintaining a safe and efficient working environment.
In sectors such as oil and gas, more frequent cleaning might be required due to the nature of materials stored. Ohio’s environmental agencies may conduct random checks to ensure compliance with set standards. Proper documentation of cleaning schedules and practices often facilitates these assessments.
Impact of Usage Frequency and Material on Cleaning Schedule
Tank cleaning schedules in Ohio can vary significantly based on the tank’s usage frequency. Tanks that are in continuous use often require more frequent cleaning to prevent residue build-up. The type of material stored also greatly affects cleaning intervals; for instance, corrosive chemicals may necessitate more frequent cleaning to prevent damage.
Industries dealing with food-grade products may adhere to stricter cleaning schedules to prevent contamination. In contrast, tanks storing inert materials might require less frequent cleaning. Understanding the nature of stored materials and their potential effects is essential in determining the appropriate cleaning frequency.
Businesses should consider the potential costs and benefits of maintaining a regular cleaning schedule. Frequent cleaning can help avoid long-term maintenance issues and extend the tank’s lifespan. A well-maintained tank not only ensures reliable operations but also aligns with Ohio’s health and safety regulations.
Effective tank cleaning practices are crucial for maintaining operational efficiency and safety in Ohio’s industrial sectors. By carefully selecting cleaning methods and adhering to regulated schedules, businesses can prevent contamination and equipment downtime. Overall, diligent tank maintenance aligns with best industry practices and supports sustainable operations.
.